|
Case
1 __ Case
2 __ Case
3
Case
Histories - FASTCO
(Courtsey of FASTCO Industries,
Inc.Grand Rapids, MI)
These case histories of forming
process development using NAGFORM sequence design program and NAGSIM.2D
simulation program are provided by our user FASTCO Industries, Grand
Rapids, MI.
Development Time:
- To cut development time, FASTCO uses
NAGFORM to give different alternative designs.Then based on
their experience, they select/modify one or two sequence designs
and finally simulate those in NAGSIM.2D to make the final selection.
Where possible, they do all this upfront before building the
tooling. An example is the part shown on right that required
a large amount of material to be upset. NAGFORM was used to
help arrive at a progression.The tooling was then designed and
the process was simulated using NAGSIM.2D software.Changes in
design were made based on the simulation. The initial setup
on the header went incredibly well. No tooling revisions were
required. Manufacturing from sample run to production went very
smoothly. Additionally, it took less than half of the time normally
required to manufacture an acceptable part.
Quality Issue:
- The picture on right shows a part that
had a quality concern. The part was not filling properly at
the corner. After the machine operators claimed that it could
not be filled, the forming operation was simulated using NAGSIM.2D.
The simulation clearly showed where the problem was, and allowed
an informed decision as to how to remove it. The tooling changes
were made and the part was formed with the revised tooling.
Picture on right shows the part filled better at the corner.
This verified the improvement as predicted by the simulation
shown.
|
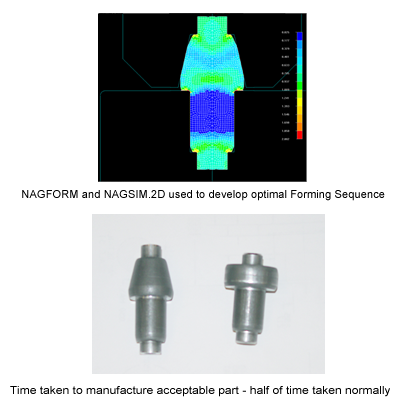
|
|